Premier Aluminum Llc for Beginners
Table of ContentsHow Premier Aluminum Llc can Save You Time, Stress, and Money.8 Simple Techniques For Premier Aluminum LlcThe smart Trick of Premier Aluminum Llc That Nobody is Talking AboutThe Single Strategy To Use For Premier Aluminum Llc
(https://linktr.ee/premieraluminum)Utilizing reduced cost and unqualified distributors can cause top quality concerns, and wasted time and cash in the lengthy run. To aid you via the procedure, right here are some points to consider when choosing the best metal casting supplier.
For instance, a company that only makes use of the investment spreading process will certainly try to sell you on why that procedure is best for your application. What if using the sand spreading process is best for you and your needs? Instead, search for a provider that provides a variety of casting processes so the finest alternative for YOU is picked
If collaborating with a single resource for all of your casting requires is very important to you, the distributor requires to be diverse in its capacities. When incorporated with other incorporated capabilities, this can help simplify and compress the supply base. When picking the right casting supplier, careful consideration should be offered to top quality, service, and price.

Unknown Facts About Premier Aluminum Llc
Purchasers significantly pick casting distributors that have machining capabilities. If the casting distributor uncovers a problem during machining, the issue is dealt with quicker with no conflict over whose mistake it is.
What do you need from your spreading supplier? Are you looking for somebody to just supply a metal component to your doorstep or do you need extra?
Others will go beyond the letter of the PO to assist you save money and time. Do you have demands for both ferrous and non-ferrous alloys? Some shops are limited or specialized. Ensure the distributor can meet all your product or alloy needs to get rid of the need for numerous vendors.
The Best Strategy To Use For Premier Aluminum Llc
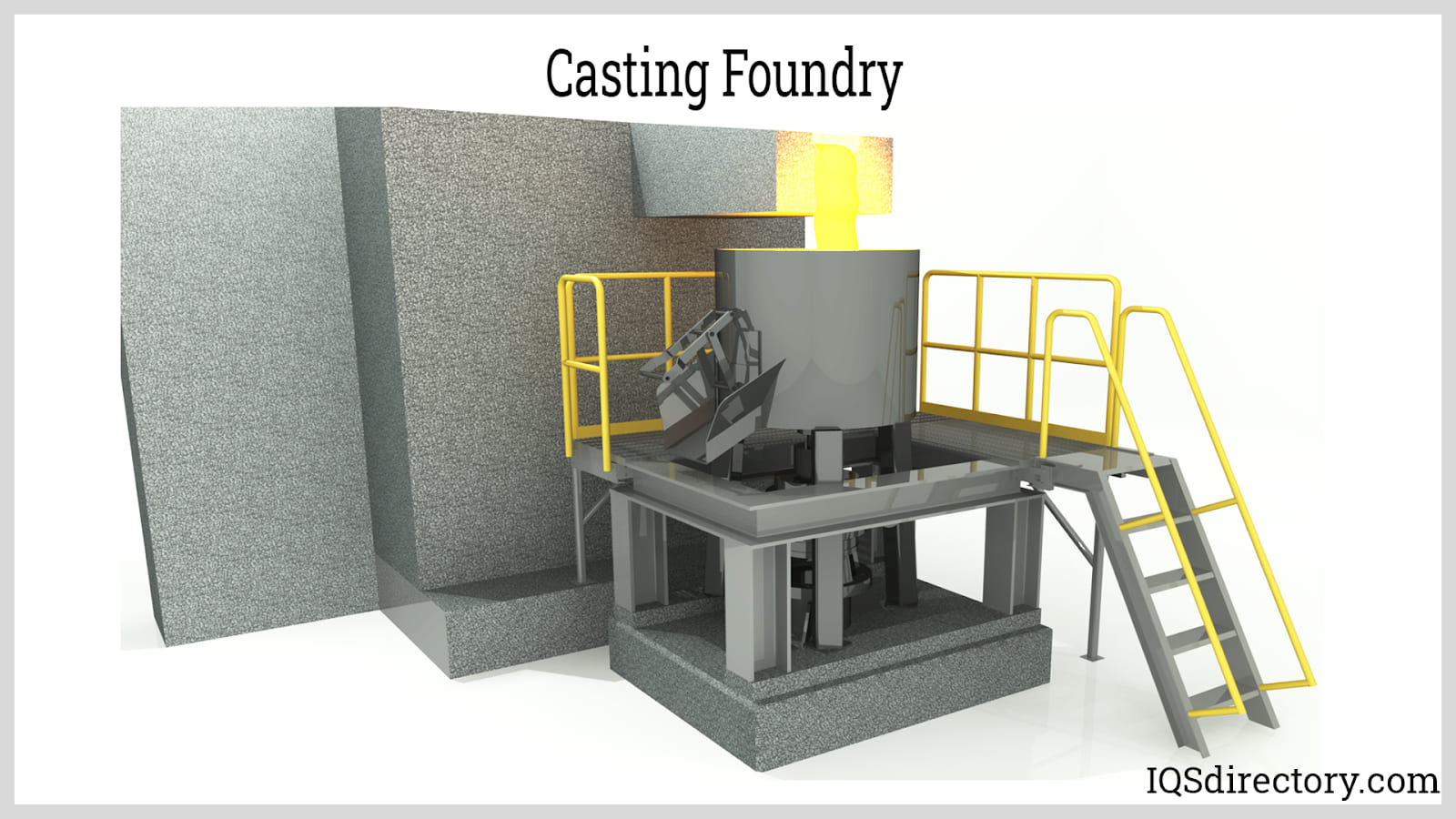
Study the supplier's site. Talk to a sales associate or organization partner.
Light weight aluminum is additionally lightweight and has good rust resistance, making it perfect for applications where weight and durability are very important factors. Furthermore, light weight aluminum casting is a cost-efficient approach of manufacturing, as it calls for much less energy and sources than various other methods. Iron spreading, on the other hand, entails putting molten iron right into a mold to develop a preferred form.
The 6-Minute Rule for Premier Aluminum Llc
Iron casting is additionally able to hold up against high temperature levels, making it suitable for use in applications such as engine components and commercial equipment. Iron spreading can be more expensive than aluminum spreading due to the higher expense of raw products and the power called for to thaw the iron. When choosing between aluminum casting and iron casting, it is very important to take into consideration the details demands of the application.
If strength and longevity are more crucial, iron casting may be the much better choice. Other elements to think about consist of expense, production volume, and lead time. To conclude, both aluminum casting and iron casting have their very own one-of-a-kind benefits and negative aspects. By very carefully thinking about the specific requirements of the application, manufacturers can pick the most effective procedure for their product.ZheJiang Dongrun Spreading Market Co,. Ltd was constructed in 1995, We have remained in the spreading sector for more than 25 years. Die casting is the name offered to the
process of producing complex metal parts via use mold and mildews of the component, also called passes away. The process makes use of non-ferrous steels which do not have iron, such as aluminum, zinc and magnesium, due to the preferable residential properties of the metals such as low weight, higher conductivity, non-magnetic helpful hints conductivity and resistance to rust. Die spreading manufacturing is quick, making high production degrees of components very easy.
It creates more elements than any various other procedure, with a high degree of precision and repeatability. To read more concerning die spreading and die spreading materials utilized in the process, kept reading. There are three sub-processes that drop under the category of die spreading: gravity die spreading (or permanent mold spreading), low-pressure die casting and high-pressure die spreading. The pure steel, likewise recognized as ingot, is included in the heating system and kept at the molten temperature of the steel, which is after that movedto the injection chamber and infused right into the die. The stress is after that kept as the metal solidifies. When the metal solidifies, the cooling procedure starts. The thicker the wall of the part, the longer the cooling time due to the amount of indoor steelthat likewise requires to cool down. After the part is fully cooled, the die cuts in half open and an ejection device pushes the part out. Following the ejection, the die is shut for the following injection cycle. The flash is the extra material that is cast throughout the process. This must be cut off making use of a trim tool to
leave just the primary part. Deburring removes the smaller pieces, called burrs, after the trimming process. The element is polished, or burnished, to provide it a smooth surface. Nonetheless, this confirmed to be an inaccurate test, since the tester might reduce into a piece and miss out on a location with porosity. Today, top makers make use of x-ray screening to see the whole inside of components without reducing into them. This enables them to more accurately accept or deny components. To get to the finished product, there are 3 primary alloys utilized as die spreading product to pick from: zinc, aluminum and magnesium. Zinc is one of the most used alloys for die spreading because of its reduced price of basic materials.